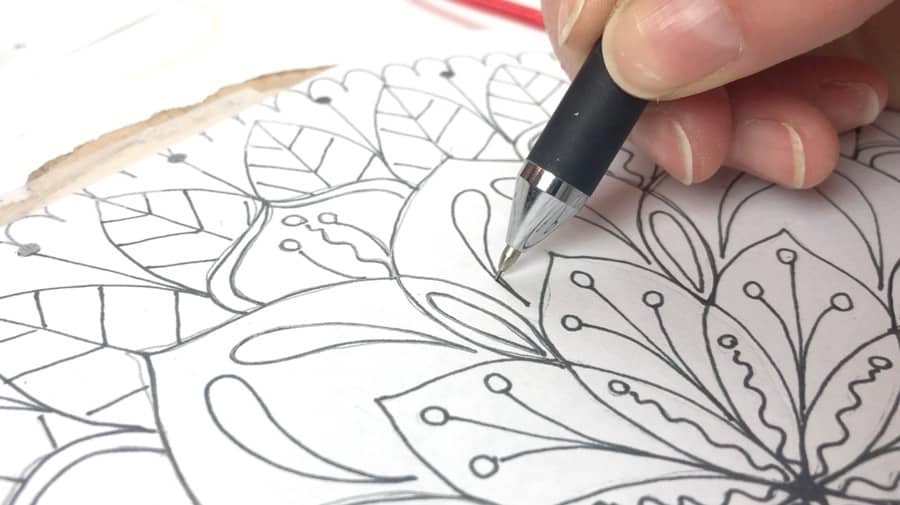
To add depth and color to your wood burning, you need to learn how to create shading points. There are three types, cone point, flow and shading points, when it comes to wood burning. Each type serves a different purpose. The cone point can be used to create fine details, small dots and outlines. The shading tip is great for filling large areas with dark colours. The flow point and mini flow points are great for making large dots. While the shading point is perfect for creating small dots and curves, the shading point works well for smaller dots. The texture ’n tone point, another type of woodburning tool, is useful for creating fine lines using a single stroke.
A wood burning shading point
A few tips will help you create a shading point when you are ready to begin woodburning your first project. First, your shading should be smooth and even. Graduations in tone should be gradual, so you should begin with a flat spoonshaped shading point to achieve a subtle transition between light and dark. This woodburning project allows you to try several pyrographic techniques.
To begin creating a shading point, you'll need an outlining tool. The outlining tool can be either a standard pen tip or a broad tip. The process is similar to tracing with a pen, but you'll need to apply more pressure for darker lines. Also, consider the angle at which your fire should be lit. The angle should be about 60 degrees. You should also turn the wood several times to get the best angle for burning.
To create a stippled effect
This technique is a great way to add depth and interest to a design. Dotting is an age-old art technique that originated in medieval art pieces. The process involves heating a bolt of metal and marking the wood with it. This can be done using a wood stove with a large tip. The tip should be clean whenever too much matter accumulates. Using a soft wood, you can create a bevel edge that evokes the appearance of the natural beauty of the wood.
Scrumbling is a way to create small, continuous circles using a pen tip. This is similar to doodling. This can be done with a wide range of pen tips. Shader points create a smooth, even fire. A shader point can be used to create texture or shading.
Adding color to wood burning
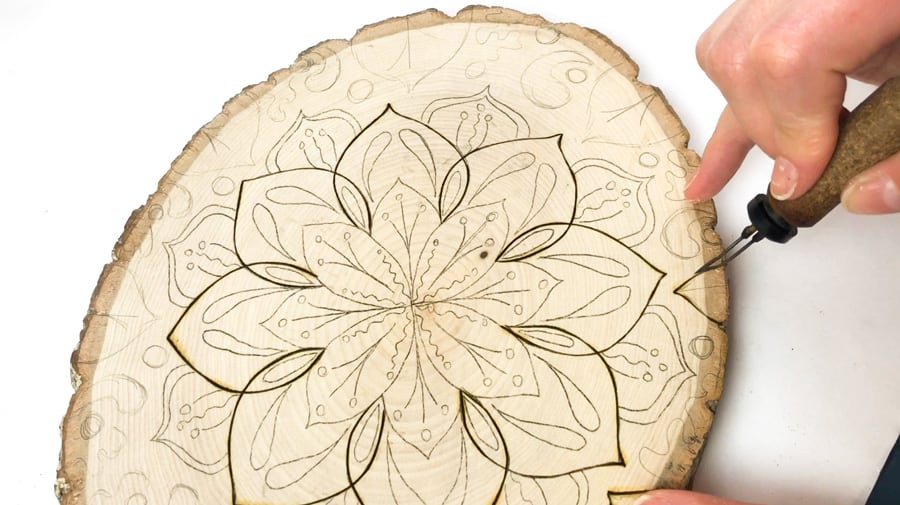
It takes careful planning to add color to wood burning. It is essential that the final product has a pleasing design. Anything with corners or sloppy edges will reflect on it. According to St. Thomas Aquinas, beauty is in the eye of the beholder, a subjective concept. However, ancient Greeks came up with a variety of design principles such as balance, repetition, proportion, contrast, unity, and symmetry.
Before adding color to your wood-burning design, you need to first decide on the background that you would like. You can use pencils (or markers), watercolors, oils paints, fabric dyes, and even oil paints. Use transparent colors to allow for sepia to shine through when using pencils. You can also use a white artist's eraser to remove excess pigment and dust. You can mix different colors together to get the desired look.
Creating a rounded tube
Pull-away is the best technique to create a rounded shape from woodburning. This technique allows you to vary the intensity of the colors from the edges to the middle of the object. The tip should be pulled away from the wood by starting at the edge. It's best to face the tip towards your artist and start at the edge.
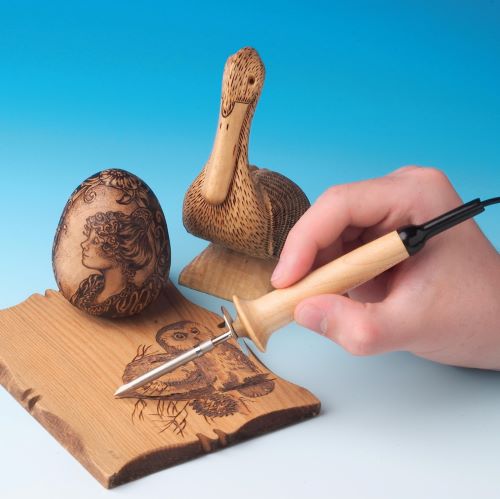
To create a rounded tube, add a base layer. The footer can be made from concrete. It will create a rounded tube at its bottom. It is also important to make sure that the bottom layer of the footer is smooth. This is the easiest way of building a footer. After it's done, you can remove the concrete forms and finish the bottom layer of the wood burning stove.
FAQ
Are you a genius in order to master woodworking?
No. Woodworking does not require any special skills. Anyone can learn to use basic powertools and techniques to create beautiful work of art.
How do I get started with woodworking?
Learning how to build furniture is the best method. You will need tools. There are bound to be mistakes. But if your persistence is consistent, you will soon master the craft.
Choose a project that interests you. It can be something as simple and small as a box, or large-scale as an entertainment center. Once you have settled on a specific project, it is time to find a woodworker in your area who is experienced in such work. Ask him or her for advice on what tools you'll need and where to find them. Perhaps you could ask if there is someone else who does this type of work.
Where can you buy hardwood lumber?
Home Depot sells hardwood lumber. They sell all kinds of wood products, including flooring, cabinets, furniture, etc.
A wide range of engineered hardwoods are also available, such as Ipe and Brazilian Cherry (Pau d'Arco), Mahogany and Swietenia Macrophylla.
These woods can also be purchased online by simply searching Google for "hardwood timber"
What woods can be used to make furniture?
Woods are classified according their hardness. Softwoods can be pine, fir or cedar. Because they are resistant, they can be used for outdoor furniture. Hardwoods include oak, maple, mahogany, and teak. Because they are not weather-resistant, they are best used indoors.
What type of tools does a carpenter use?
Carpenters use a hammer as their most common tool. The hammer is used to pound nails into wood. A hammer is used to hold pieces together during a project. Other tools include clamps, pliers, screwdrivers, measuring tape, pencils, saws, drills, and wrenches.
What is the difference between a hobbyist or a professional woodworker, and how can you tell?
Hobbyists love making things from wood while professionals are more concerned with the quality of their work. Hobbyists often take pride in the creations they make and often share them to family and friends. Professionals spend hours researching design ideas before starting to work on a project. They'll pay great attention to details, from choosing the most suitable materials to finishing the work perfectly.
What amount of money do I need to get started with my business?
Since every project differs, it is impossible to give exact numbers. These factors will help you get an estimate of how much money is needed.
-
Material cost
-
Tools and equipment
-
Time spent working on this project
-
Hourly rate
-
What amount of profit can you expect to make?
-
You can hire help, regardless of whether you have a plan.
It's a good idea for beginners to start with small projects like frames and boxes. As you gain experience, you'll be able to tackle more complex projects.
Statistics
- Most woodworkers agree that lumber moisture needs to be under 10% for building furniture. (woodandshop.com)
- The best-paid 10 percent make $76,000, while the lowest-paid 10 percent make $34,000. (zippia.com)
- The U.S. Bureau of Labor Statistics (BLS) estimates that the number of jobs for woodworkers will decline by 4% between 2019 and 2029. (indeed.com)
- In 2014, there were just over 237,000 jobs for all woodworkers, with other wood product manufacturing employing 23 percent; wood kitchen cabinets and countertop manufacturing employing 21 percent. (theartcareerproject.com)
External Links
How To
How to make wood joints
This tutorial will demonstrate how to join two pieces together of wood. We will use the "pockethole joint," which means that we drill holes in the wooden pieces and then glue them together. This method is great if your wood's straight and smooth. You might consider dowel joinery if your wood isn’t straight or flat. Here are the steps
-
Drill Pocket Hole Joints. You will need to measure and mark the exact location of your pocket hole joint. Next, drill 3/4 inch holes in each end of each piece using a handheld drilling machine or jigsaw.
-
Sand Smooth. Sanding the wood's edges will help ensure that the joint won't split later.
-
Glue the two sides of the wood together. Apply glue on both sides of the wooden plank. Allow the wood to rest for five minutes before clamping it together.
-
Secure the pieces together. After the glue has dried completely, you can clamp the pieces together until they are flush.
-
Trim Joinery. Trim any excess wood surrounding the joint once the glue has dried completely.
To be able to turn the pieces inside-out, leave enough room between them.