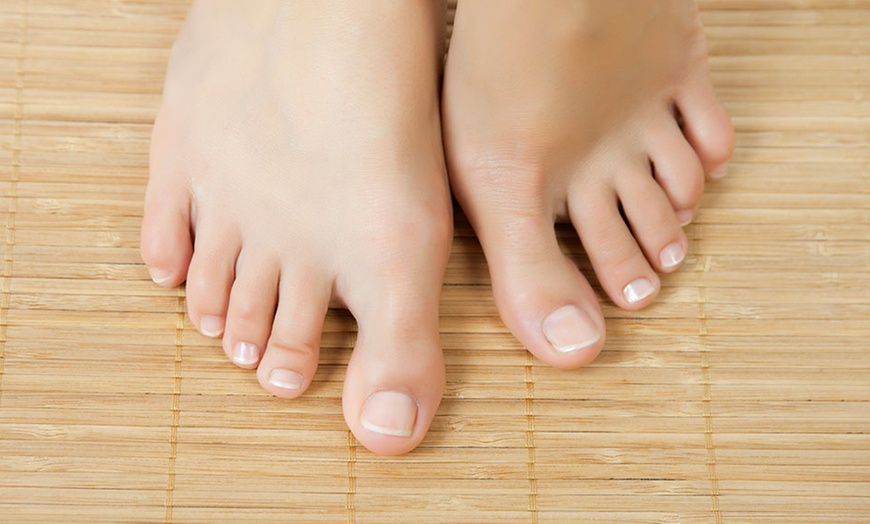
Many woodworkers have asked this question: How do you create perfect mitre joint? We will be discussing different methods to make them. These include closing miter gaps, gluing mitre joint, creating hidden spline, and closing miter gaps. Then we will show you how to create perfect 45-degree angles. We'll also cover how to install mitre joints that are already glued. Continue reading for more information.
Gluing mitre joints
Following these tips makes gluing mitre corners easy. Prepare the mitered corners prior to gluing. If you are gluing a piece of wood that will come apart later, it is important to align the miter edges. After assembling the mitre joint, you can apply some wood adhesive to the mitred corners. Use a damp cloth to wipe off excess adhesive.
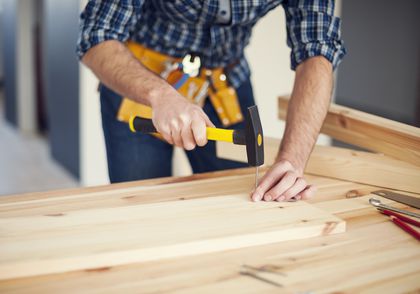
Closing a Miter Gap
There are many ways to close miter gaps in woodworking projects. Using a rounded object such as a screwdriver shank or nail-set cone can help you close the gap. To give your paint a toothy look, you can also use sandpaper. You can force the filler in the gap with a knife if you don't have the money to purchase a round tool.
Creating a hidden spline
A hidden spline can be used to create mitre joints which are flush with the mitered edges. This can be achieved by creating a slot just below the heel on the mitered face. The slot should equal or exceed the thickness of the workpiece. This will allow for the maximum length of the spline. Also, remember to plane your spline stock before you insert it into the mitre joints.
Getting perfect 45-degree angles
Although it is possible to get perfect angles of 45 degrees at miter joints, it can be challenging if the pieces are not exactly 90 degrees. There are two possible reasons. One reason is that pieces might be too long. The second problem is that the blade could not be perpendicular on the cut surface. This can cause compound angles. In either case it is vital to correctly scribe any angles.
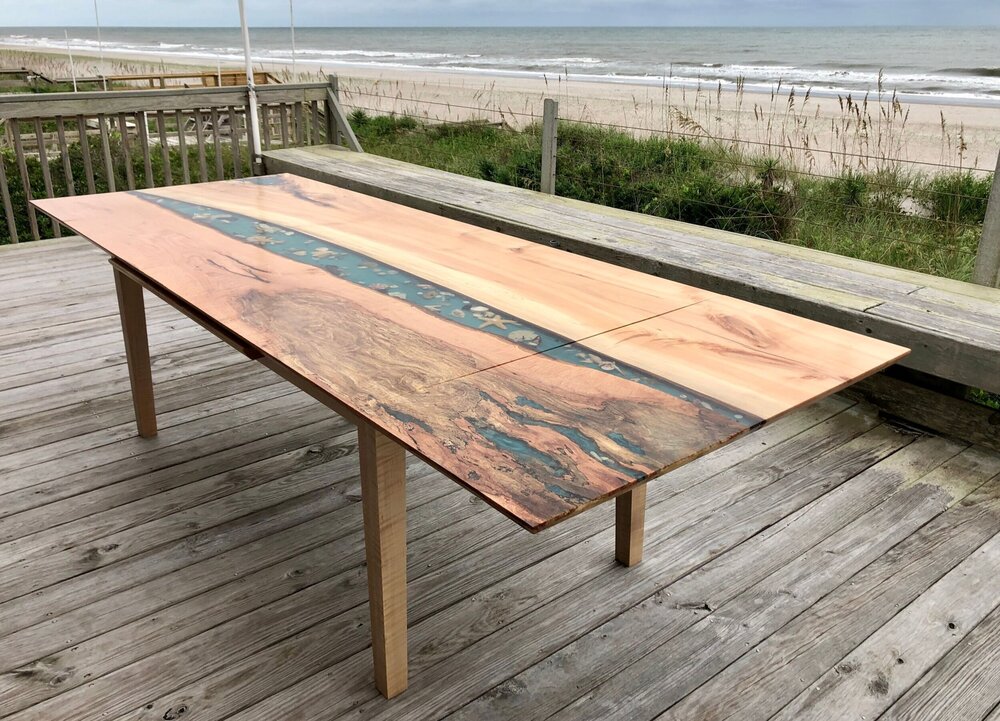
Using DOMINO wood jointing system
Domino wood jointing is the best choice for miter joints in your next project. This jointing system is a cross between a biscuit and round dowel. It is strong enough to keep the pieces in position and can be easily shaped and cut to fit the precise dimensions. You can quickly make mitered panel joints with the DOMINO wood joining system.
FAQ
Which material would you recommend for woodworking lessons?
Start with softwoods such as pine and poplar. After you are comfortable with the softwoods, move to hardwood.
How do I get started as a woodworker?
Woodworking takes practice and patience. It takes time and practice to master the various techniques and tools required for woodworking.
There are many woodworking tools on the current market. Some people prefer using power tools while others prefer hand tools.
While you have the option to pick what you like, it is essential that you get the right tool for the job. Start with a basic set if you don’t have any previous experience.
You might also want to learn how a router works, which allows you to cut wood into intricate shapes. These routers can be purchased at most hardware and home improvement stores.
How much money will I need to get started?
There are no exact numbers because every project is different. Consider these factors if you need to estimate the amount of money that you will require.
-
Cost of materials
-
Tools and equipment
-
The time spent on the project
-
Hourly rate
-
What is your expectation for profit?
-
It doesn't matter if your goal is to hire help
Start small, if possible. You can make simple boxes or picture frames if you're just getting started. As you gain experience, you'll be able to tackle more complex projects.
Statistics
- If your lumber isn't as dry as you would like when you purchase it (over 22% in Glen Huey's opinion…probably over 10-15% in my opinion), then it's a good idea to let it acclimate to your workshop for a couple of weeks. (woodandshop.com)
- In 2014, there were just over 237,000 jobs for all woodworkers, with other wood product manufacturing employing 23 percent; wood kitchen cabinets and countertop manufacturing employing 21 percent. (theartcareerproject.com)
- Most woodworkers agree that lumber moisture needs to be under 10% for building furniture. (woodandshop.com)
- The U.S. Bureau of Labor Statistics (BLS) estimates that the number of jobs for woodworkers will decline by 4% between 2019 and 2029. (indeed.com)
External Links
How To
Tips for driving a nail in wood
The first step in driving a nail into wood is to choose the correct size and type of hammer. The most common types of hammers are claw hammers, sledgehammers, mallets, ball peen hammers, and hatchets. Each type has its strengths and weaknesses. A claw hammer works well when you're trying to hit nails with a heavy hammer. However it is difficult to precisely control where the blow hits. A sledgehammer is great for hitting large areas at once, but it's too heavy to use effectively for smaller tasks.
Place your hand flat on the side of your chosen hammer so that the handle rests in your palm. You can grip the handle with your fingers, but not so tight that it causes injury. The hammer should be held straight up with your wrist relaxed. You should then swing the hammer straight up, keeping your wrist relaxed. The impact of the hammer hitting the nail should be felt. If you're having trouble getting the hang of swinging a hammer, practice with a block of wood until you get the rhythm down.
You can now drive the nail by holding the hammer to your body. Position the nail, so it's perpendicular to the surface of the wood. Keep your attention on the tip. Then, swing the hammer forward. Next, follow the motion of your hammerhead. Continue this motion several times, slowly increasing the speed of each swing. Try adding power to your swings when you've mastered the technique. Hold the hammer high above your shoulders and pull it down. This will help you put more energy behind each of your moves.
Once you've made the first nail hole, take out the hammer. To pull out the remaining nails, use a screwdriver or pry bar. You should ensure that the nails are flush with the board's surface to avoid splitting the wood.