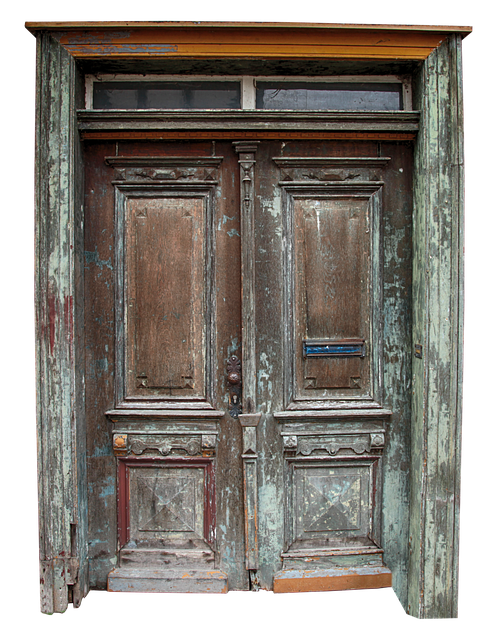
There are many online videos that show woodcarving. Many people prefer watching Ian's videos as they demonstrate techniques step-by-step. His videos are available as downloadable video files. Plans and photographs are also included. All buyers must be able view MPG videos as well as JPG images. He also offers books that will teach you how to carve different materials. Ian Norbury's Fundamentals of Woodcarving is an example.
Woodcarving Fundamentals
A fundamentals class is a good idea for anyone new to woodcarving. This class will teach you the fundamentals of carving and is tailored to the level of experience of each student. Before you can learn more advanced techniques, safety, tools and wood will be covered. The class will cover carving a human face, an eagle or Christmas ornament. Additionally, you will learn about grain direction as well as clever ways to cleanly remove wood.
Woodcarving classes might be a good option if your desire to carve flowers and fruits is strong. It's not difficult to learn the fundamentals if you have a natural talent for the craft. No matter your skill level, you will learn the design process and techniques in a relaxed and fun environment. Woodcarver and thirty-year veteran can tell you that woodcarving's foundation is finding a teacher who can help you become a master woodcarver.
Ian Norbury
Ian Norbury's woodcarving videos are like peering over the shoulder at a master carver. Each video walks you through the process step-by-step, demonstrating the techniques he has developed in his fifty years of carving. These videos offer detailed instruction and a money back guarantee. They can be downloaded at any time, and you can watch them as many times or less as you like.
You can use the DVD for reference or as a training tool. The videos offer step-bystep instructions as well clips of Ian Carving. You can view the entire process from beginning to end. Ian's teaching method is also easy to follow, and he shows you how to carve a harlequin, or depict a character from a myth. You have over two hours worth of instructional videos that will help you improve your technique.
Frank Russell
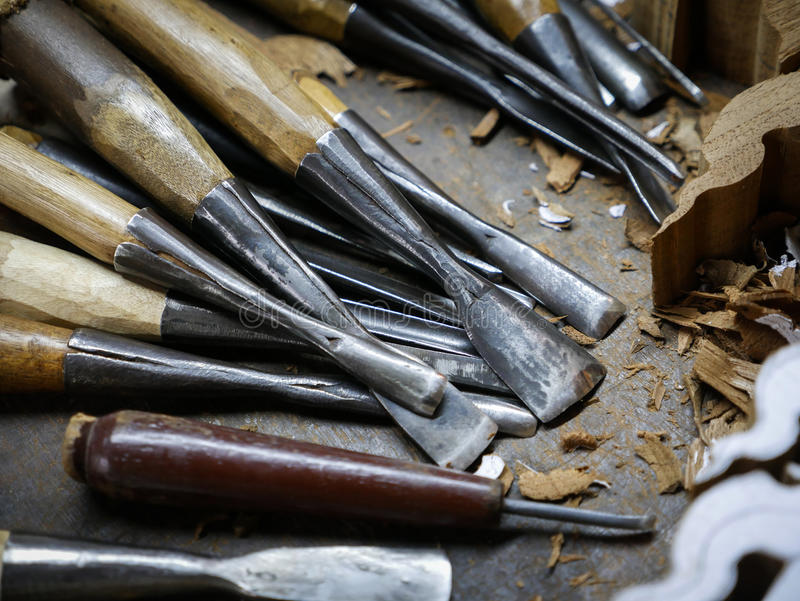
Frank Russell's woodcarving videos are great for beginners or intermediate carvers. His techniques include woodcarving animals and birds as well as plants. He also shows how to shape and clean bits. Videos show the process of carving as well as how to create visual concepts. Frank Russell's videos can be viewed online or on DVD. If you're looking for a comprehensive guide to carving birds and other animals, Fur, Feathers, and Fins are ideal.
Frank Russell's videos on woodcarving are great resources for both beginning and advanced carvers. These videos contain detailed step-by-step instructions for beginners and tips for advanced carvers. They're filmed with Foredom Woodcarving Kits and feature a variety of tools, including Typhoonburs and CeramCut Blue abrasive points. There is also a Cotton Tail Rabbit carving tutorial.
Scott Phillips
If you're looking for more information on woodcarving, you may want to watch Scott Phillips woodcarving videos. The PBS show, "American Woodshop," features Scott and his woodcarving skills. He shares about his first woodcarving encounter, using his father's costly walnut boards. Scott also talks about how his love for baseball inspired the creation of his first decorative jewelry container. Scott's woodcarving videos are not the only ones he has made. Scott also wrote a book on shuttle history. Scott will also be chronicling the history in his book "Remove Before Flight." He still makes other types of furniture occasionally, such as clocks and Adirondack chair, even though his woodcarving career has taken off.
Kevin Coates
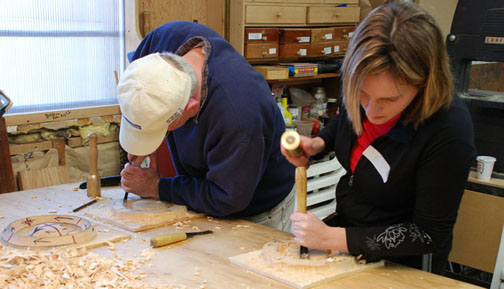
Kevin Coates' videos on woodcarving are great for those who enjoy carving. He has a YouTube channel with almost seven million views and 26,000 subscribers. His videos inspired many woodcarvers to make their own videos. Watch them to learn how to carve your own piece of art. These videos feature carvings made by Kevin Coates or other well-known carvers. If you're looking for some inspiring carving videos, look no further.
FAQ
What woods are suitable for making furniture?
Woods are classified by their hardness. Softwoods can be pine, fir or cedar. They are great for outdoor furniture as they resist rot. The hardwoods include teak, maple, mahogany and oak. They can't withstand the elements outside so they're best kept indoors.
Does it take a genius to make woodworking work?
No. Woodworking does not require any special skills. Anyone can learn to use basic powertools and techniques to create beautiful work of art.
How do you calculate woodworking costs?
It is essential to calculate costs as accurately as possible when pricing any project. You should always try to make sure that you are getting the best deal on materials. Also, consider all other factors that can affect the price of your projects such as skill level, experience, time and cost. Our guide to the average household DIY task price will give you an idea of how much it costs to complete different types of woodwork projects.
What is the average time it takes to finish furniture?
It depends on the type of wood you choose, the complexity of the design, and the amount of finishing you apply. Hardwoods require more care than softwoods. Hardwoods can also be more costly than softwoods. They last longer and are more resistant to moisture. The average time it takes to finish furniture is one week to three weeks.
What is the hourly rate for a woodworker?
The hourly rate for a professional woodworker varies depending on many factors, including skill level, experience, availability, location, and other variables.
A skilled woodworker can expect an hourly rate of $20-50.
A less skilled woodworker might charge as low as $10 per hour.
Statistics
- Overall employment of woodworkers is projected to grow 8 percent from 2020 to 2030, about as fast as the average for all occupations. (bls.gov)
- The U.S. Bureau of Labor Statistics (BLS) estimates that the number of jobs for woodworkers will decline by 4% between 2019 and 2029. (indeed.com)
- If your lumber isn't as dry as you would like when you purchase it (over 22% in Glen Huey's opinion…probably over 10-15% in my opinion), then it's a good idea to let it acclimate to your workshop for a couple of weeks. (woodandshop.com)
- Most woodworkers agree that lumber moisture needs to be under 10% for building furniture. (woodandshop.com)
External Links
How To
Tips on how to drive a nail in wood
To drive a nail into wood, the first step is to select the right size and type hammer. The most common types of hammers are claw hammers, sledgehammers, mallets, ball peen hammers, and hatchets. Each kind of hammer has its own advantages and disadvantages. A claw hammer, for example, is the best choice if you need to hit nails hard. However, it's not easy to know exactly where the impact will land. A sledgehammer allows you to hit large areas simultaneously, but it is too heavy and cumbersome to use for small tasks.
After you've chosen the right tool, hold your hand flat to the handle so it rests comfortably in one of your palms. You can grip the handle with your fingers, but not so tight that it causes injury. You should hold the hammer straight-up, with your wrist still relaxed. Then swing the hammer back toward the ground, aiming for the center of the nail. You should feel the impact of your hammer hitting the nail. Try practicing with a block to help you master the art of swinging a stick.
When you're ready to start driving the nail, hold the hammer in front of you close to your body. Place the nail so that it is perpendicular with the wood's surface. Keep your eyes on the tip. Swing the hammer forward, and then move the hammerhead. You can repeat this several times, increasing your swing speed. Try adding power to your swings when you've mastered the technique. Then, raise the hammer from your shoulder to bring it down. You'll have more energy to work with.
Once you've made the first nail hole, take out the hammer. Use a pry bar or screwdriver to pull out the rest of the nails. Keep the nails heads in line with the surface of the board to prevent splitting the wood.