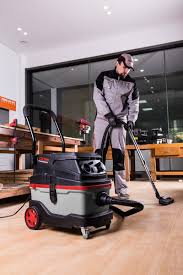
Philip Moulthrop began turning wood in 1979, learning his craft from his father, Ed Moulthrop. He uses a hand-forged, chainsaw and lathe to roughen out the green portions of trees from the Southeast. The bowl is then refined on the lathe and finished with several coats. The entire process can take from four months up to one year. Once completed, the bowls may be purchased or given to friends and family as gifts.
Philip Moulthrop
Phillip Moulthrop bowl, a magnificent red leopard maple vessel is available. The process of wood turning, which he developed, has been a family tradition for three generations. In addition to their own creations, Philip Moulthrop's bowls are part of the permanent collections of several prominent museums and private collections around the world. Below are some of the most well-known pieces. Continue reading for more information about this gifted artist.
Philip Moulthrop, an American painter, was born in 1947. He started his education in general arts when he was just 20 years old and quickly developed a passion for woodworking. He purchased his first lathe when he was 16 years old and gradually increased his equipment. His techniques were successful and he was able to produce beautiful vessels. This attracted the attention not only of the art community but also the President of the United States. After his work was recognized, he began selling his pieces at the local craft fairs and galleries and began receiving international recognition.
Matt Moulthrop
The Matt Moulthrop Boulbows are a fine example of Georgia’s rich wood-turning heritage. The artist was born in Atlanta and received his BA and MBA from Georgia Tech. He spent a few years working in 9-to-5, but he never lost his passion for woodturning. In fact, he received recognition nationally for his bowls. His works are on display at the ASU Art Museum as well the Carter Center and Racine Art Museum.
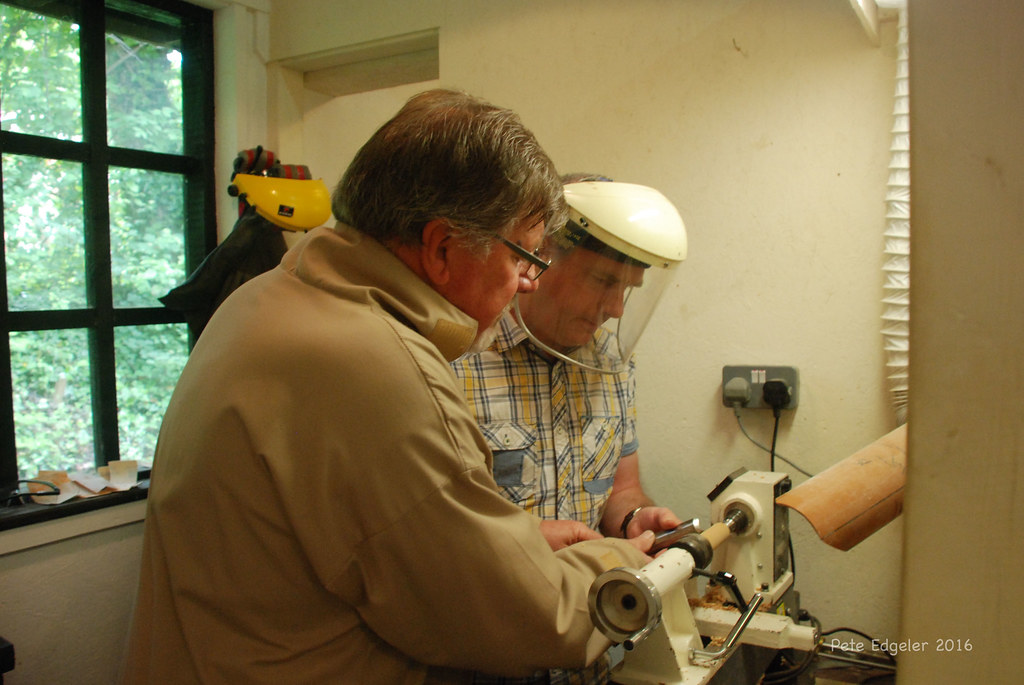
The Moulthrops were recognized as world-class woodturners. Their works have been placed in prominent collections across the United States and around the globe. Moulthrops' pieces are on display at the Renwick Gallery of the National Museum of American Art. Collectors from all over the globe have taken to heart his bowls. He signed each photographer's copy of the family book during a Smithsonian photo shoot.
Ed Moulthrop
Moulthrop began to turn bowls around 1970s. Soon after, he received a scholarship at Princeton University to study architectural design. Moulthrop spent a year in Vietnam and then resigned as an architect to pursue woodturning. His large-scale turned bowls received international recognition and are currently held in museums such the Museum of Arts and Design and White House Collection of American Crafts. These bowls were made from domestic woods, and are polished to a clear shine.
This rare Ed Moulthrop bowl is nine inches in diameter by fourteen inches high and made of wild cherry. These wood bowls can also be bought at Gump’s San Francisco. There are many other pieces of Ed Moulthrop's wooden bowls on display. The best way for you to learn more about this artisan is by visiting the exhibition. He also publishes a beautiful catalogue of his work. Although it is possible for you to buy the bowls from museums it is much better to see his studio.
The Eagle & Phenix Dam Series
This limited edition series is made with wood from the Eagle & Phenix Dam. They are handmade by Philip Moulthrop, local artists. They are open for bidding during regular museum hours. Some bowls will be up for auction live.
The Moulthrop families has played a significant role in Georgia's development of wood-turned bowls. The Moulthrop family has been making bowls for over 50 years. Three generations have contributed to the creation of this museum. These pieces are prized for their large sizes and smooth, polished surfaces. This exhibit features his mosaic bowl technique that involves glue and thin branches adhering to a turned dish.
Matt Moulthrop's work
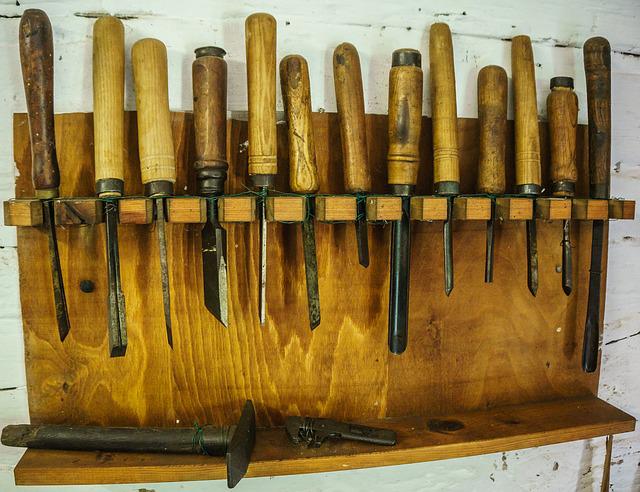
Matt Moulthrop was the son of Philip Moulthrop. From a young age, his father taught him woodturning and he has never stopped loving it. Matt earned his BA at Georgia Tech and his MBA from Georgia Tech. After that, he turned his attention to woodworking as a profession. He is the third generation of woodworkers. His work has been featured in numerous prominent art institutions, such as the ASU Art Museum (now the Carter Center). He is currently working on commemorative pieces for the Georgia Tech Alumni Association's 100th anniversary.
Georgia is not home to the wood he turns. He also travels to other countries to search for unusual wood. He turns trees from around the world, using tools and a hand-forged lathe to create unique pieces. He uses wood from the Southeast as well as exotic locations like underwater forests and volcanoes to create his pieces. You will love his work!
FAQ
How can a novice woodworker make it big?
Many people learn how to make furniture in order to set up an online business. There are other ways to make money if you're just starting out building furniture than selling on Etsy. You could sell at craft fairs or local events. Or you could offer workshops for others who want to learn how to build their own furniture. Consider offering your services if you have previous experience as a builder or carpenter.
Where do I start with woodworking?
It is best to actually build furniture to learn how to make it. While you will need tools and make mistakes, you will eventually master the art of building furniture.
Begin by choosing the project that you want to finish. You could make something as simple or complex as a box. Or you could build a whole entertainment center. Once you've decided on a project, find a local woodworker who specializes in that kind of work. Ask your local woodworker to help you determine the right tools for you and where they are located. You might even ask whether there's someone else you can talk to who does this kind of work.
What kinds of woods are good for making furniture?
Woods are classified based on their hardness. Softwoods are pine, cedar and cypress. Because they are resistant, they can be used for outdoor furniture. These hardwoods include maple, mahogany and teak. Because they are not weather-resistant, they are best used indoors.
Where do I get my woodworking supplies?
You can find everything you need in many places. You could also visit hardware stores in your area or shop online at Amazon.com.
You might also consider flea markets and garage sale for any old furniture or other materials you could reuse.
Statistics
- The best-paid 10 percent make $76,000, while the lowest-paid 10 percent make $34,000. (zippia.com)
- In 2014, there were just over 237,000 jobs for all woodworkers, with other wood product manufacturing employing 23 percent; wood kitchen cabinets and countertop manufacturing employing 21 percent. (theartcareerproject.com)
- If your lumber isn't as dry as you would like when you purchase it (over 22% in Glen Huey's opinion…probably over 10-15% in my opinion), then it's a good idea to let it acclimate to your workshop for a couple of weeks. (woodandshop.com)
- Average lumber prices rose about 600 percent between April 2020 and May 2021. (familyhandyman.com)
External Links
How To
How to make wood joints
This tutorial will help you join two pieces of wooden together. We will be using the "pocket-hole joint", which involves drilling holes in wood and then gluing them together. This method is great if your wood's straight and smooth. You might consider dowel joinery if your wood isn’t straight or flat. Here are the steps
-
Drill Pocket Hole Joints. First, measure the area where you wish to place the pocket joint. Next, drill 3/4 inch holes in each end of each piece using a handheld drilling machine or jigsaw.
-
Sand Smooth. You can sand the edges of the wood to ensure that it doesn't split.
-
Glue together. Apply glue to both the ends of the wood. Let it sit for about 5 minutes before clamping the pieces together.
-
Clamp the Pieces Together. After the glue has dried thoroughly, secure the pieces so that they are flush.
-
Trim Joinery. Trimming the joinery after glue has completely dried.
To be able to turn the pieces inside-out, leave enough room between them.